The main development direction of the future of injection mold

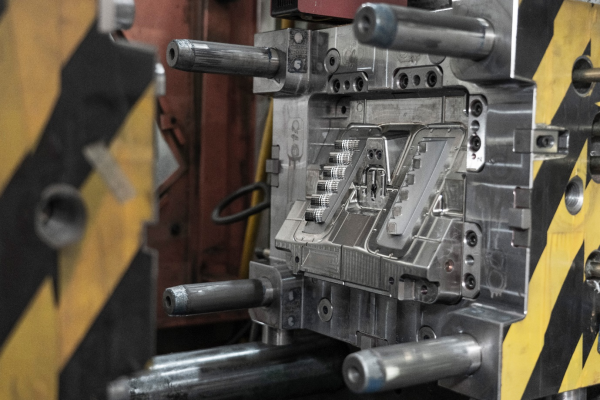
Zhongshan, Guangdong, China, 19th Jun 2023 – In recent years, the injection mold industry has become increasingly challenging to operate in. Intense competition has driven down the prices of injection mold orders, prompting some individuals to consider leaving the industry. As a mold-making provider and an injection molding manufacturer with over a decade of experience in the mold industry, Prototool is enduring the tests of time, much like mud and sand in a vast river.
However, Prototool remains confident in the potential of this industry. While acknowledging the challenges and fierce competition that the mold industry faces is necessary, it is essential to recognize the opportunities and growth prospects within this field. By adopting strategic planning, fostering innovation, and prioritizing customer needs, the mold industry can not only overcome these challenges but also flourish and make significant contributions to the manufacturing sector.
Prototool has identified several future directions for mold development and eagerly seeks to share these insights with industry peers.
A: High Precision:
One of the key areas of focus in the future development of Injection Mold is achieving high precision. Precision plays a crucial role in industries such as automotive, aerospace, and electronics, where tight tolerances are required. Advancements in technology and manufacturing techniques enable mold development with exceptional precision.
These molds can produce components with minimal dimensional variations, ensuring superior quality and performance of the final product. Integrating advanced software, simulation tools, and quality control measures enables mold manufacturers to consistently achieve the desired precision levels.
B: High Efficiency:
Efficiency is another critical aspect driving the future development of injection molds. Manufacturers continually seek ways to streamline production processes, reduce cycle times, and optimize resource utilization. Advancements in mold design, material selection, and cooling systems contribute to improved efficiency.
For instance, conformal cooling channels allow for more uniform cooling, reducing cycle times and enhancing productivity. High efficiency also means high automation. Integrating automation in mold manufacturing and injection molding processes further boosts efficiency by minimizing human intervention and maximizing production output.
C. Advanced designing and manufacturing technology:
With advancements in new injection mold technologies, many molds that were once considered complex and difficult to achieve can now be simplified. Additionally, structures that were once thought impossible can now be accomplished. These developments present new opportunities and challenges for the injection molding industry.
Specifically, mold designers and makers with expertise in these new injection mold designs and manufacturing technologies will have a competitive advantage. It is important to remember that the injection mold industry has always relied on technology and industry expertise to maintain its standing and reputation.
D.Integration of product development and tooling:
The integration of product development and tooling is a significant direction for the future development of injection molds. Traditionally, product design and mold design were considered separate entities, resulting in potential issues during the manufacturing stage. However, with technological advancements, manufacturers can seamlessly integrate product and mold design.
This integration enables early collaboration between designers and mold engineers, ensuring that molds are designed with manufacturability in mind. By considering moldability during the product design phase, potential design flaws and manufacturing challenges can be identified and addressed early, resulting in more efficient and cost-effective mold development.
In this way, the future development of injection molds is headed towards achieving high precision, high efficiency, advanced manufacturing process, and product development and tooling integration. Technological advancements, manufacturing techniques, and the growing need for improved quality and productivity drive these directions. As these developments continue to unfold, the injection molding industry will witness enhanced capabilities, streamlined processes, and the ability to manufacture complex and high-quality products more efficiently than ever before.
Media Contact
Organization: Prototool Manufacturing Limited
Contact Person: Ray Liu
Website: https://prototool.com/
Email: sales@prototool.com
Contact Number: +86 18928167001
Address: 88 West Shagang Road, Gangkou Town
City: Zhongshan
State: Guangdong
Country: China
Release Id: 1906234225